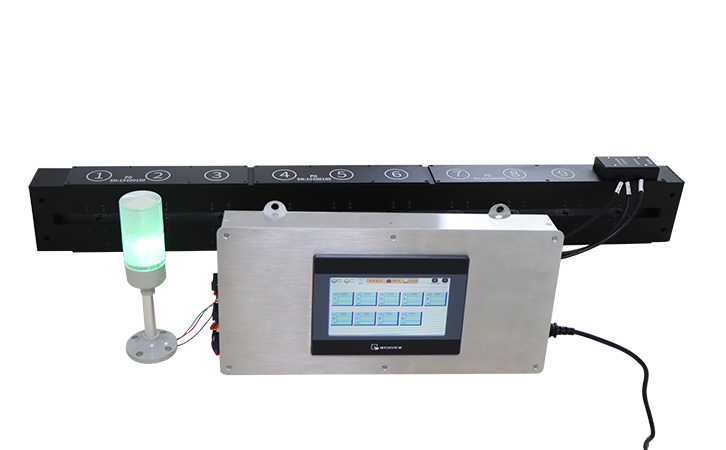
86152 Vacuum Coating Thickness Measuring System
Online monitoring of material uniformity and coating thickness
Free to choose the number of test points, 45 test points can be customized at most
Two-way RS485 communication interface, MODBUS communication protocol
Strong anti-interference, data is stable
86152 vacuum coating thickness measuring system works in the principle that the transmittance (optical density) of the material is proportional to the coating thickness. The uniformity of the material is achieved by monitoring the optical transmittance (optical density) of the material. As long as the light can pass through the material, the product quality can be controlled by monitoring the transmittance (optical density). Because it can monitor two parameters of both transmittance and optical density, it is also called optical density online detector. This vacuum coating thickness measuring system is widely used in concentration vacuum coating machine, glass coating production line, window film coating line and other occasions.
86152 Vacuum Coating Thickness Measuring System Introduction
The user can freely choose the number of test points. The figure below shows the appearance of the vacuum coating measuring system with 9 test points. The actual length of the device is based on the number of customized test points.
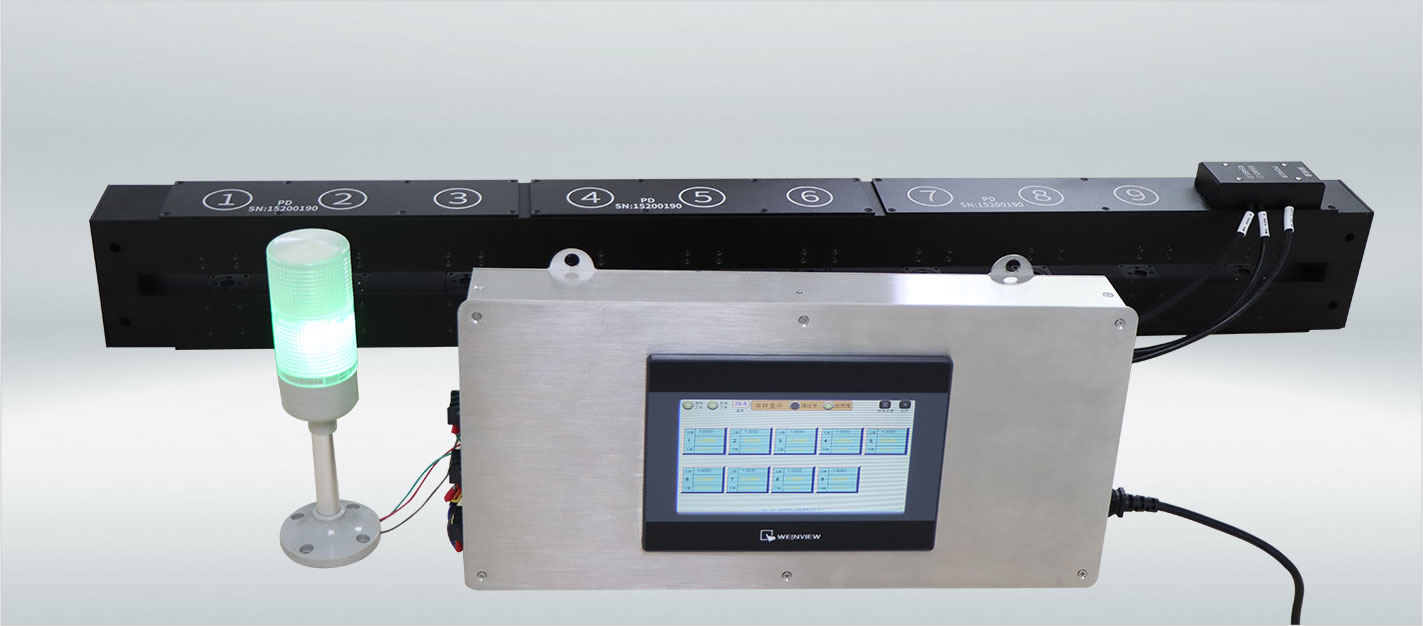
The instrument provides dual RS485 communication interface and standard MODBUS communication protocol, which is convenient for communication with PLC, Single Chip Microcomputer, human-machine interface, kingview, computer and so on. The optical density data can be read on the coating machine to realize control automation (closed-loop control).
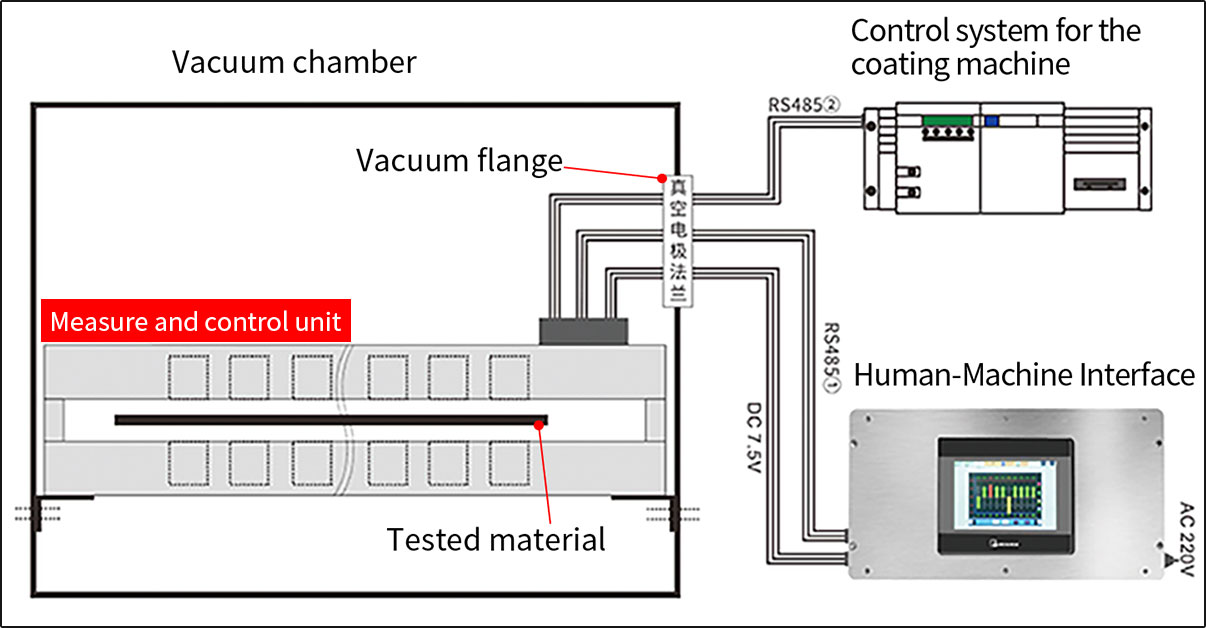
System Composition
The equipment is mainly divided into three parts: measure and control unit, human-machine interface, computer real-time monitoring software (optional).
Measurement and control units
They mainly includes light source probe, receiving probe, controller, aluminum profile frame
Human-machine interface
It mainly includes human-machine interface, power supply and stainless steel box
Computer real-time monitoring system (optional)
Real-time monitoring of the data, including real-time display, histogram, setting of upper and lower limits, real-time curve and alarm when the limit is exceeded. The transmittance and optical density display can be switched freely
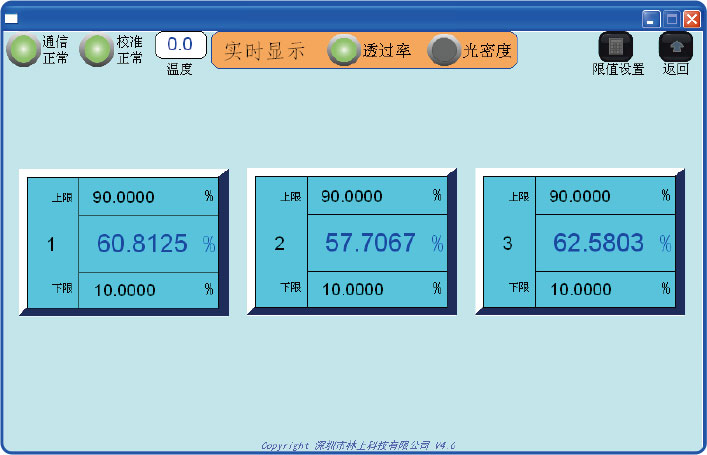
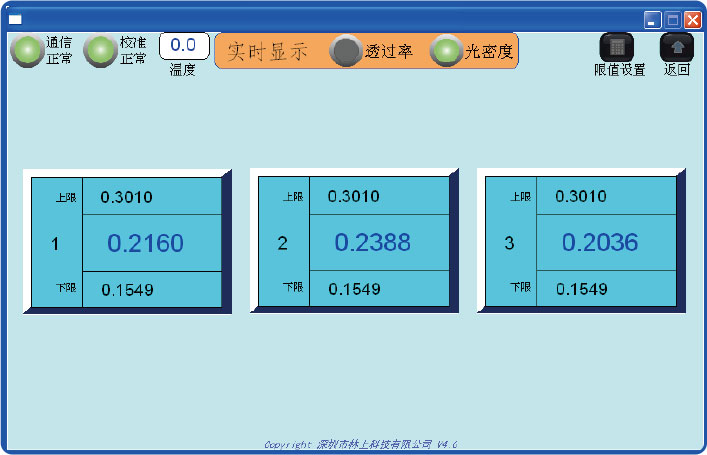
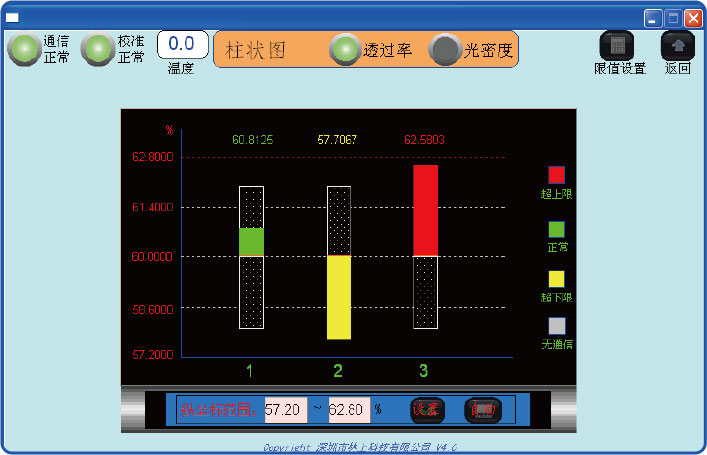
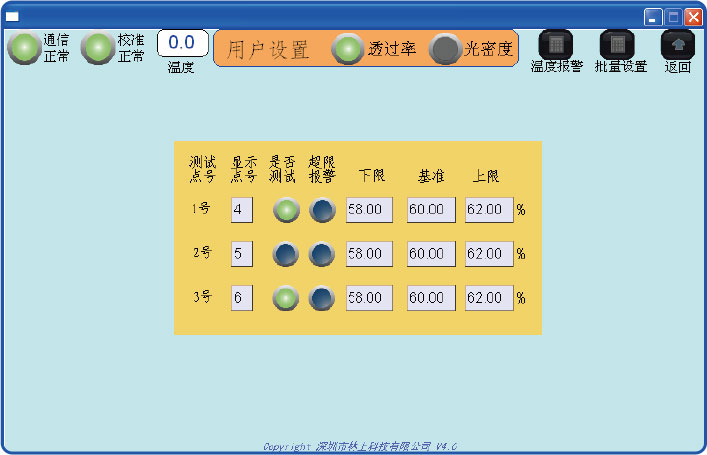
Control console and installation method
The controller and the test probe are embedded in the control console and only need to fix the control console during installation. Each device is equipped with a bracket, which is customized according to the actual installation needs of customers. The installation diagram of the control console is as follows

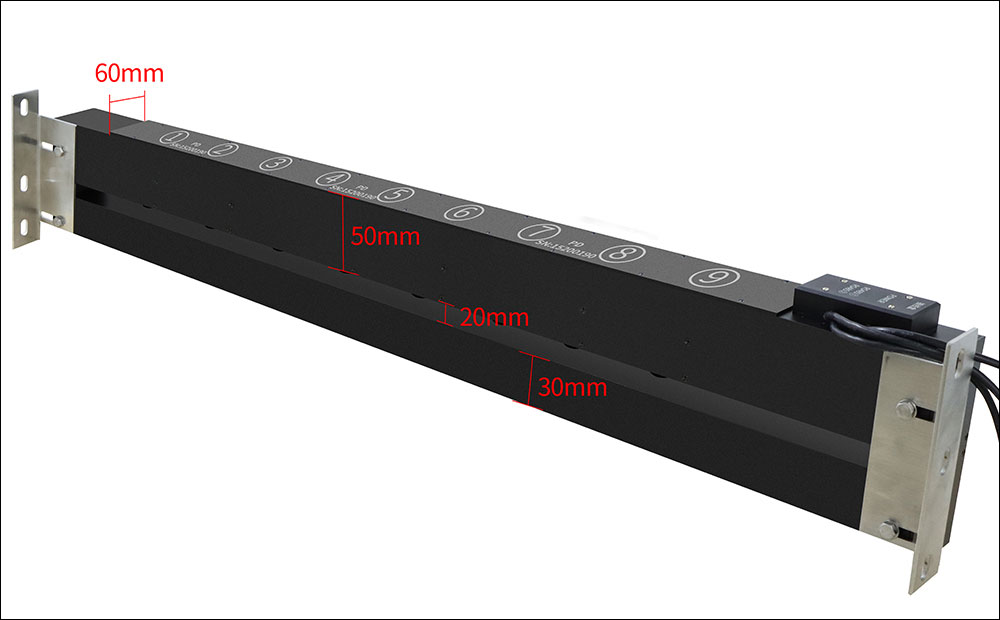
Features
1.The ultra-small controller is embedded in the console. It is easy to use and install. We only needs to connect 6 wires.
2.The instrument use optical non-contact measurement, without direct contact with the test material. It will not cause damage to the tested material.
3.The vacuum coating thickness measuring system has high measurement accuracy.
4.The instrument use modular design, single point is removable, which is convenient for future maintenance.
5.With dust-proof design, dust does not affect the inside of the gyroscope. Customers just need to clean the front glass of the probe.
6.Use RS485 interface + MODBUS communication protocol. The instrument can achieve closed-loop control with the coating machine.
7.The instruemtn has over-limit alarm function and can intelligently control production quality. The instrument can reduce dependence on manual operation and improve production efficiency and quality.
System Parameters
Parameters | 86152 |
---|---|
Test Wavelength (optional) | Green light: 530nm; Infrared: 850nm |
Measuring Spot | 5mm |
Transmittance Measurement Accuracy | ±1% |
Transmittance Resolution | 0.005% |
Optical Density Measurement Range | 0.00 OD - 5.00 OD |
Optical Density Resolution | 0.01 OD for 0.00-3.00 OD 0.05 OD for 3.00-5.00 OD |
Maximum Measurement Points | 45 points |
Distance Between Adjacent Probe | Minimum distance of 35mm |
Distance Between Receiving Probe And Light source probe | 20mm |
Temperature Range | -10°C - 60°C |
Storage Temperature | -20°C - 70°C |
Relative Humidity | less than 85%, no condensation |
Data Refresh Cycle | Normal mode 300ms/ Fast mode 100ms |
Communication Interface | Dual RS485 |
Communication Protocol | MODBUS protocol |
Dimension | 80mm(W)*180mm(H)*L (Customized) |
Vacuum Flange Electrode Cores | 6 ( RS485①+DC7.5V) 9 ( RS485①+ RS485②+DC7.5V) |
Power Supply | 220V 0.2A AC/50Hz |